Auto Parts
Introduction:
Vacuum forming is a widely used manufacturing process in the automobile industry for producing various plastic components. This cost-effective and versatile technique involves heating a plastic sheet and then using vacuum pressure to shape it over a mold. Vacuum formed plastic parts find applications in a wide range of areas within the automotive sector, offering several advantages over other production methods. This article will explore the various applications and advantages of vacuum formed plastic parts in the automobile industry.
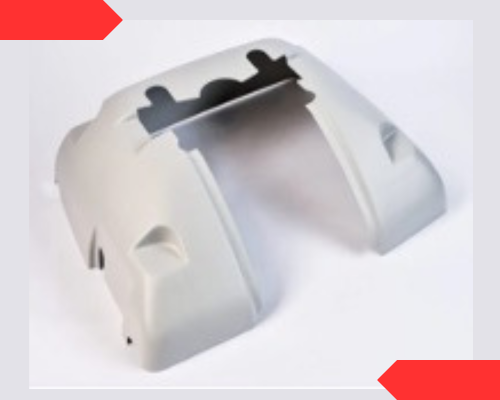
Interior Components:
1.1 Dashboard and Instrument Panels:
Vacuum formed plastic parts are extensively used in the manufacturing of dashboard and instrument panels. The process allows for the creation of complex shapes, contours, and integrated features such as air vents, cup holders, and control panel cutouts. Vacuum formed dashboard and instrument panels offer design flexibility, weight reduction, and cost-effectiveness compared to traditional injection molding methods.
1.2 Door Trims and Panels:
Vacuum formed plastic parts are also utilized for manufacturing door trims and panels. These components enhance the aesthetics and functionality of the vehicle’s interior. Vacuum forming allows for customization, precise fitment, and the integration of features such as speaker grilles, window switches, and armrests. The lightweight nature of vacuum formed door trims contributes to improved fuel efficiency and handling.
1.3 Headliners and Sun Visors:
Headliners and sun visors, which provide interior insulation and sun glare reduction, can be efficiently produced using vacuum forming. The process allows for the creation of lightweight and durable components with integrated features like lighting fixtures and mounting points. Vacuum formed headliners and sun visors offer enhanced acoustic insulation, design flexibility, and cost-effectiveness.
1.4 Center Consoles and Glove Boxes:
Center consoles and glove boxes are crucial storage and control units within the vehicle’s interior. Vacuum formed plastic parts are commonly used for manufacturing these components due to their ability to produce complex shapes, seamless finishes, and integrated functionalities such as cup holders, USB ports, and touchscreen displays. Vacuum formed center consoles and glove boxes offer customization options, reduced weight, and improved durability. The diverse application of vacuum-formed parts in the automotive industry, specifically focusing on tractors, trucks, trains, ambulances, and driver and passenger cabins. Vacuum forming is a versatile manufacturing process that utilizes heated plastic sheets to form complex shapes by creating a vacuum between the mold and the sheet. This cost-effective technique offers numerous benefits such as lightweight construction, design flexibility, and improved efficiency. The following sections will delve into the advantages of vacuum-formed parts, their specific applications in different automotive vehicles, and the resulting benefits for manufacturers and end-users.
The automotive industry demands robust and efficient components to meet the requirements of various vehicles. Vacuum forming has emerged as a viable solution for manufacturing lightweight, durable, and cost-effective parts. This section provides an overview of the vacuum forming process and its advantages.
Vacuum Forming Process
2.1 Heating and Stretching
2.2 Molding and Cooling
2.3 Trimming and Finishing
Advantages of Vacuum Formed Parts
3.1 Lightweight Construction
3.2 Design Flexibility
3.3 Cost-effectiveness
3.4 Enhanced Efficiency and Performance
Applications of Vacuum Formed Parts
4.1 Tractors
4.2 Trucks
4.3 Trains
4.4 Ambulances
4.5 Drivers and Passengers Cabin
Tractors
5.1 Benefits of Vacuum Formed Parts
5.2 Applications in Tractors
5.3 Examples and Case Studies
Trucks
6.1 Benefits of Vacuum Formed Parts
6.2 Applications in Trucks
6.3 Examples and Case Studies
Trains
7.1 Benefits of Vacuum Formed Parts
7.2 Applications in Trains
7.3 Examples and Case Studies
Ambulances
8.1 Benefits of Vacuum Formed Parts
8.2 Applications in Ambulances
8.3 Examples and Case Studies
Drivers and Passengers Cabin
9.1 Benefits of Vacuum Formed Parts
9.2 Applications in Cabin Components
9.3 Examples and Case Studies
Conclusion
The utilization of vacuum-formed parts in the automotive industry offers numerous advantages, ranging from lightweight construction to enhanced efficiency. Tractors, trucks, trains, ambulances, and drivers and passenger’s cabins benefit from the cost-effectiveness and design flexibility provided by vacuum-formed components. As the automotive industry continues to evolve, vacuum forming will play a pivotal role in meeting the industry’s demand for reliable, efficient, and innovative solutions.
In conclusion, this paper highlights the various applications of vacuum-formed parts in the automotive industry, specifically focusing on tractors, trucks, trains, ambulances, and driver and passenger cabins. The benefits of vacuum forming, including lightweight construction, design flexibility, and cost-effectiveness, make it an ideal choice for manufacturers and end-users alike. With ongoing advancements in vacuum forming technology, the automotive industry can expect further improvements in efficiency, performance, and overall customer satisfaction.