Door Trims
Automobile door trims play a crucial role in enhancing the aesthetics, functionality, and comfort of a vehicle’s interior. Manufacturers employ various production methods to create these door trims, and one popular technique is vacuum forming. This section will discuss the advantages of utilizing vacuum forming in the manufacturing of automobile door trims.
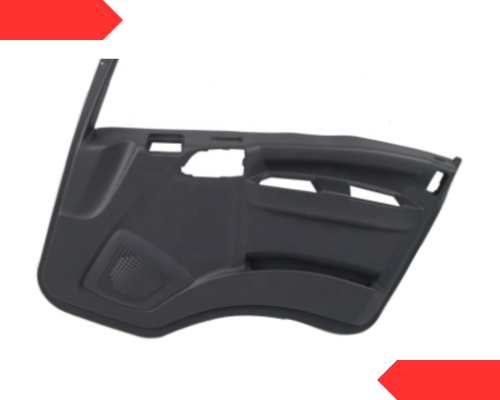
Cost-effectiveness:
Vacuum forming offers a cost-effective solution for producing automobile door trims compared to other manufacturing processes. The initial tooling costs for vacuum forming are relatively low, making it an economical choice for both small and large-scale production. Additionally, vacuum forming allows for efficient material usage, minimizing waste and reducing overall production costs.
Design Flexibility:
Vacuum forming provides a high degree of design flexibility, enabling manufacturers to create intricate and customized door trims. The process allows for the production of complex shapes, curves, and contours, providing designers with the freedom to explore innovative and visually appealing designs. Manufacturers can easily incorporate unique features such as embossed patterns, textures, and brand logos into the door trims, enhancing the overall aesthetics of the vehicle’s interior.
Lightweight Construction:
Automobile manufacturers are increasingly focused on reducing vehicle weight to improve fuel efficiency and performance. Vacuum-formed door trims contribute to lightweight construction due to their inherent properties. The process utilizes lightweight plastic materials, resulting in lighter door trims compared to alternatives such as injection molding or metal fabrication. The reduced weight not only enhances fuel efficiency but also improves handling and reduces overall vehicle weight, leading to enhanced performance.
Durable and Resilient:
Vacuum-formed door trims exhibit excellent durability and resilience, making them suitable for the demanding automotive environment. The plastic materials used in vacuum forming are impact-resistant and capable of withstanding daily wear and tear. They are less prone to scratches, dents, and fading, ensuring that the door trims maintain their aesthetics and functionality over an extended period. Moreover, vacuum-formed parts can be engineered to have increased rigidity and structural integrity, providing additional strength to the door trims.
Easy Installation and Integration:
Vacuum-formed door trims are designed with ease of installation and integration in mind. Manufacturers can tailor the shape and dimensions of the door trims to ensure a perfect fit for specific vehicle models. This precise fit simplifies the installation process, reducing assembly time and costs for automotive manufacturers. Additionally, vacuum-formed door trims can be manufactured with integrated features such as mounting clips, fastening points, and wiring channels, facilitating seamless integration into the vehicle’s interior assembly.
Enhanced Acoustic and Thermal Insulation:
Door trims manufactured through vacuum forming can contribute to improved acoustic and thermal insulation within the vehicle cabin. The plastic materials used in the process possess inherent sound-dampening properties, reducing external noise intrusion into the cabin. Furthermore, vacuum-formed door trims can incorporate additional insulation layers or foam backing, enhancing thermal insulation and creating a more comfortable and quieter cabin environment.
Customization and Personalization:
Vacuum forming allows for easy customization and personalization of automobile door trims. Manufacturers can offer a wide range of color options, surface finishes, and textures to match the customer’s preferences and vehicle branding. This customization capability enables automakers to differentiate their vehicles and cater to various market segments, enhancing customer satisfaction and brand loyalty.