Vacuum Formed Plastic Parts
Team Insulink provides a complete range of vacuum forming solutions, all under one roof. In order to replace “Sheet Metal Components”, “Injection Moulded Parts”, “Packing Cushions & Buffers” with vacuum formed parts, we conceptualize basic design of the part, according to customers requirement. We also make in-house moulds, jigs & fixtures and extruded sheets. This all enable us to produce and supplies quality parts to our esteemed customers on time.
Using the expertise of our experience design engineers, we support our customers by designing suitable and optimized packing design. This enable our customers to ensure safe delivery of their products to users and reduce field defects / returns. This not only reduces customer complains but also help generating more sales and profits.
Our vacuum forming solutions as replacement to “Sheet Metal Components”, “Injection Moulded Parts”, “Packing Cushions & Buffers” are cost – effective and ideal for low batch productions, prototype making and new product launch. Vacuum formed parts are generally 3 – 4 times stronger than Injection moulded parts and its initial tooling cost is 75% lower as compared to Injection moulds.
Understanding and prioritizing the need to reduce plastic footprints gradually and replace plastic with bio-degradable / oxy – biodegradable / compostable alternative materials Insulink has developed and offer aforesaid materials to provide immediate solutions to our customers.
Our vacuum-formed products find application across a wide range of industries. From automotive and electronics to medical and packaging, we cater to diverse sectors with versatile solutions. Our engineers extends to creating components, enclosures, trays, and displays that meet the specific needs of each industry. Whether it’s enhancing product functionality, improving visual appeal, or optimizing packaging efficiency, our vacuum-formed products deliver exceptional value to our customers businesses.
To stay at the forefront of the industry, we constantly push boundaries and investigate new possibilities in vacuum forming. Our committed research and development staff works tirelessly to improve our processes, test new materials, and integrate cutting-edge procedures. This dedication to innovation enables us to provide innovative and proactive solutions that assist our customers in differentiating their products in the market.
Technical Specifications
Category | Material Type | Length (in MM) Min - Max |
Width (in MM) Min - Max |
Thickness (in MM) Min - Max |
Color Customization |
---|---|---|---|---|---|
Thin Shheet | Polystyrene - PS/HIPS | 25-600 | 25-670 | 0.2-2.0 | Yes, Subject to MOQ |
ABS | 25-600 | 25-670 | 0.2-2.0 | Yes, Subject to MOQ | |
PP | 25-600 | 25-670 | 0.2-2.0 | Yes, Subject to MOQ | |
PET | 25-600 | 25-670 | 0.2-2.0 | Yes, Subject to MOQ | |
PVC | 25-600 | 25-670 | 0.2-2.0 | Yes, Subject to MOQ | |
Thick Sheet | Polystyrene - PS/HIPS | 50 - 2500 | 50 - 1500 | 2.0 - 6.0 | Yes, Subject to MOQ |
ABS | 50 - 2500 | 50 - 1500 | 2.0 - 6.0 | Yes, Subject to MOQ | |
PP | 50 - 2500 | 50 - 1500 | 2.0 - 6.0 | Yes, Subject to MOQ | |
HDPE | 50 - 2500 | 50 - 1500 | 2.0 - 6.0 | Yes, Subject to MOQ |
- For HIPS, PP, PET, PVC - Available in Anti-Static, ESD, Conductive
- For ABS & HDPE - Available in only Anti - Static
- Anti-Static ( Surface Resistivity : (10^9-10^11 Ω)
- ESD : Electrostatic Discharge (Surface Resistitvity : 10^6-10^9 Ω)
- Conductive (Surface Resistivity : (10^2 - 10^5 Ω)

Auto Parts
Introduction:
Vacuum forming is a widely used manufacturing process in the automobile industry for producing various plastic components. This cost-effective and versatile technique involves heating a plastic sheet and then using vacuum pressure to shape it over a mold. Vacuum formed plastic parts find applications in a wide range of areas within the automotive sector, offering several advantages over other production methods. This article will explore the various applications and advantages of vacuum formed plastic parts in the automobile industry.
Read More Send A Enquiry
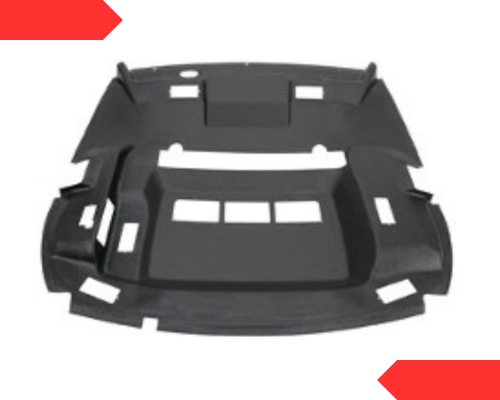
Drone Body Parts
Drone body parts made through vacuum forming are typically made from thermoplastic materials such as ABS (Acrylonitrile Butadiene Styrene) or PET (Polyethylene Terephthalate). Vacuum forming is a manufacturing process that involves heating a sheet of plastic material until it becomes pliable, then placing it over a mold and using a vacuum to draw the material down onto the mold. This creates a three-dimensional shape that conforms to the mold.
Read More Send A Enquiry
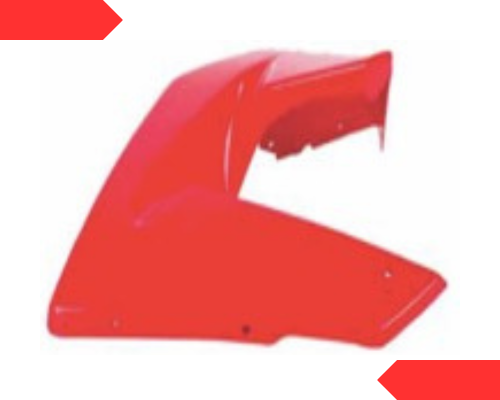
EV Body Parts
It is worth noting that vacuum forming can produce parts with a uniform wall thickness, which can result in a more consistent and predictable strength compared to injection molding. This is because vacuum forming uses a single mold to create the part, while injection molding uses a complex system of molds and channels to inject the material into the mold. This can result in variations in wall thickness and other factors that can affect the strength of the final product.
Read More Send A Enquiry
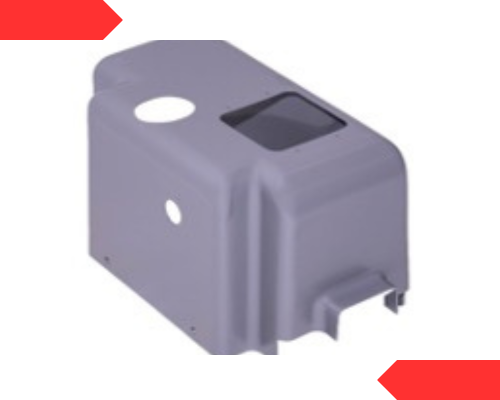
Locomotive Body Parts
Vacuum forming is a manufacturing process that involves heating a plastic sheet until it becomes pliable, then stretching it over a mold and using a vacuum to draw the plastic tightly against the mold. This process can be used to create a variety of parts for trains and locomotives, including interior and exterior components.
Read More Send A Enquiry
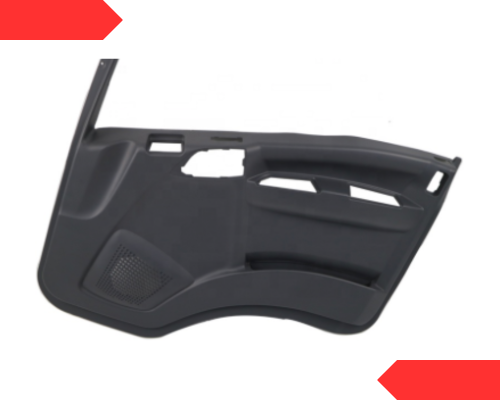
Door Trims
Automobile door trims play a crucial role in enhancing the aesthetics, functionality, and comfort of a vehicle's interior. Manufacturers employ various production methods to create these door trims, and one popular technique is vacuum forming. This section will discuss the advantages of utilizing vacuum forming in the manufacturing of automobile door trims.
Read More Send A Enquiry

Cabin Headliners
Introduction:
The headliner in an automobile cabin plays a significant role in enhancing the interior aesthetics, acoustics, and comfort for both drivers and passengers. Vacuum forming is a popular manufacturing process utilized to create headliners. This section will discuss the advantages of using vacuum forming in the production of automobile cabin headliners.
Read More Send A Enquiry
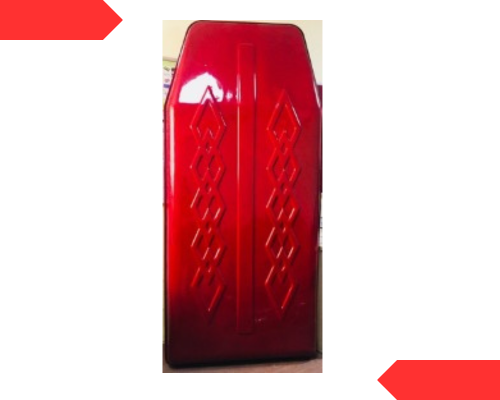
E-Rickshaw Roof
Electric rickshaws, also known as e-rickshaws or electric three-wheelers, have gained popularity as an eco-friendly and cost-effective mode of transportation. The head roof in an electric rickshaw serves as a protective cover for the passengers and the driver. Vacuum forming, using ABS plastic, is a commonly employed manufacturing process for creating head roofs. This section will outline the advantages of using vacuum forming to produce electric rickshaw head roofs made of ABS plastic.
Read More Send A Enquiry